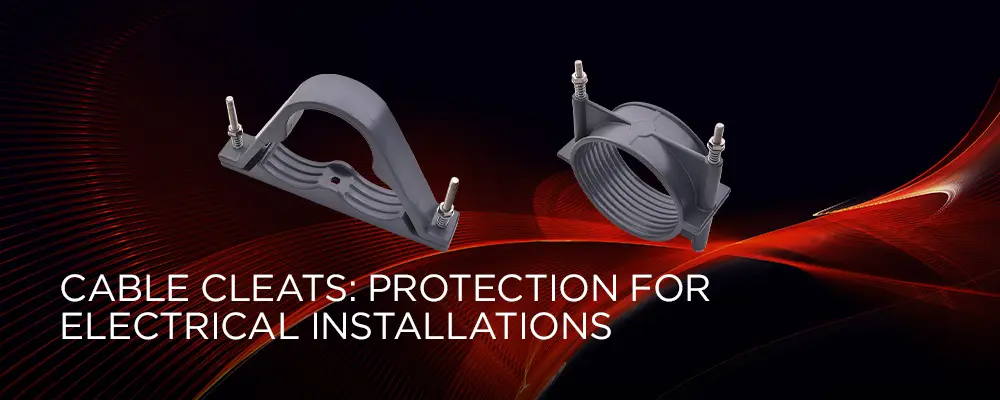
Electrical installations are vital to ensuring uninterrupted power supply across industries, commercial setups, and households. To maintain the safety and stability of these systems, cable cleats play a crucial role. These simple yet essential components provide mechanical support and secure cable management, ensuring cables remain safely positioned and protected during electrical surges, faults, or environmental disturbances.
In this comprehensive guide, we will explore what cable cleats are, their applications, types, and the key factors to consider when choosing the right cleat for your electrical systems. We’ll also highlight Atlas Metal Industries Pvt Ltd’s commitment to providing durable and high-performance cable cleats for your installation needs.
Cable cleats are mechanical devices designed to hold and secure electrical cables in place. They provide restraint and protection to cables, particularly in environments where electrical faults, mechanical stress, or environmental factors could cause displacement.
Cable cleats are manufacture generally from materials such as stainless steel, aluminum, or flame-retardant plastics. Their primary role is to ensure cable stability, prevent movement, and reduce the risk of damage or short circuits.
By choosing the appropriate cable cleat, electrical engineers can maintain safe installations and prevent costly downtime or electrical hazards.
Cable cleats are used in various applications to secure and protect cables in electrical systems. Their key functions include:
- Cable Management: Cleats hold cables firmly in place, ensuring they remain organized and secure.
- Mechanical Protection: During short circuits or electrical surges, cleats prevent cables from excessive movement, reducing the risk of damage.
- Fire Safety: Cleats designed with flame-retardant materials help prevent fire from spreading through cable runs.
- Environmental Protection: For outdoor or harsh environments, specialized cleats offer protection against weather, moisture, and corrosive elements.
From industrial power stations to data centers, cable cleats are indispensable for maintaining electrical system integrity.
In electrical systems, cable cleats provide essential protection and management in various environments:
- Power Distribution Networks: Cleats secure heavy-duty cables used in power transmission.
- Industrial Facilities: Trefoil arrangements using trefoil cable cleats prevent electromagnetic interference in high-voltage installations.
- Renewable Energy Systems: Cable cleats ensure cable stability in solar, wind, and hydroelectric power setups.
- Marine and Offshore Installations: Corrosion-resistant aluminium cable cleats are ideal for harsh environments.
By securing cables effectively, cleats minimize the risk of electrical faults, ensuring system reliability.
Understanding different types of cable cleats is essential for choosing the right product for your installation. The most common types include:
1. Single Cable Cleats
- Designed for securing individual cables to walls, ceilings, or mounting structures.
- Ideal for installations where cables run separately to reduce electromagnetic interference.
2. Trefoil Cable Cleats
- Specifically designed for three-phase systems where cables are arranged in a triangular formation.
- Trefoil cable cleats reduce electromagnetic interference and maintain equal cable spacing for optimal performance.
3. Aluminium Cable Cleats
- Lightweight yet strong, aluminium cable cleats are corrosion-resistant and ideal for outdoor installations.
- Suitable for both single and bundled cable arrangements.
4. Multicore Cable Cleats
- Designed to secure multiple cables grouped together in compact installations.
- Suitable for control panels, switchgear, and building management systems.
Choosing the appropriate cable cleat type ensures efficient cable management and reliable protection for electrical installations.
Selecting the right cable cleat is crucial for ensuring the safety and performance of electrical systems. Consider the following factors when choosing a cleat:
- Cable Size and Type: Measure the diameter of your cables to select a cleat that fits securely.
- Environmental Conditions: Use corrosion-resistant materials like aluminium cable cleats for outdoor installations.
- Short-Circuit Performance: Ensure the cleat can withstand high mechanical forces during electrical faults.
- Mounting Surface: Choose cleats that align with the mounting structure (wall, ceiling, or ladder).
- Compliance Standards: Select cleats that adhere to industry safety and performance standards.
By carefully evaluating these factors, you can ensure a secure and efficient cable management solution for your installation.
When installing cable cleats, following best practices enhances system safety and longevity. Key safety tips include:
- Correct Positioning: Ensure cleats are spaced evenly to prevent cable sagging or excessive strain.
- Material Selection: Use flame-retardant or corrosion-resistant cleats for enhanced durability in hazardous environments.
- Secure Fastening: Tighten bolts and screws adequately to prevent loose connections that may cause vibrations or displacements.
- Regular Inspection: Periodically check cleats for signs of wear, corrosion, or damage to ensure long-term stability.
By implementing these safety measures, you can maintain a secure and efficient electrical system.
Cable cleats are indispensable for safeguarding electrical installations by securing and stabilizing cables in various environments. Whether you require trefoil cable cleats, aluminium cable cleats, or other specialized options, Atlas Metal Industries Pvt Ltd offers durable and high-performance solutions to meet your needs.
Explore Atlas Metal’s extensive range of cable cleats for superior protection in industrial and commercial applications. Contact at sales@atlasmetalind.com or +91-288 2730 944. today for expert guidance and top-quality products.
How does cable cleat installation improve system safety?
Proper cable cleat installation ensures cables remain firmly in place, reducing the risk of short circuits or mechanical damage.
Are aluminium cable cleats suitable for outdoor installations?
Yes, aluminium cable cleats are corrosion-resistant and ideal for outdoor environments exposed to weather elements.
What are trefoil cable cleats used for?
Trefoil cable cleats are designed for three-phase systems to maintain cable spacing and minimize electromagnetic interference
Can cable cleats be used in hazardous environments?
Yes, specialized cable cleats with flame-retardant or corrosion-resistant materials are suitable for hazardous conditions.
Where can I find reliable cable cleats for my project?
Atlas Metal Industries Pvt Ltd offers a comprehensive range of cable cleats designed for optimal performance in electrical installations.